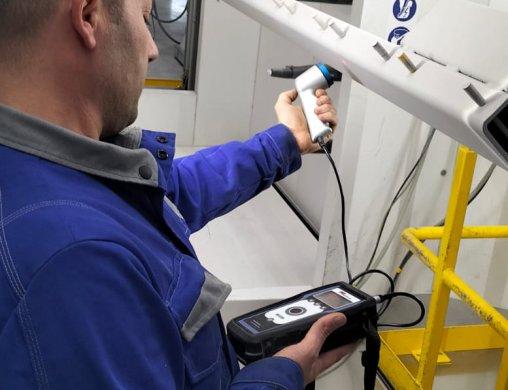
Dass bei diesen der Teufel manchmal im Detail steckt, musste das Unternehmen bei einem großvolumigen Auftrag schmerzhaft erfahren. Durch einen vom Kunden vorgeschriebenen, neuartigen Pulverlack war die geforderte Schichtdickte nicht immer optimal einzuhalten. Da die applizierten Bauteile aber erst nach dem Einbrennen geprüft werden konnten, war erheblicher Ausschuss die Folge.
Um vor derart verlustreichen Aufträgen zukünftig gefeit zu sein, suchte man nach einer Lösung, die die Schichtdicke deutlich früher im Prozess messen kann – und fand diese im neuen PaintChecker mobile von OptiSense.
Millionen-Investition in das OberflächenBeschichtungszentrum
Der Ruf der Textilbranche nach immer größeren und leistungsfähigeren Anlagen hat auch die Nachfrage beim Maschinenhersteller Brückner verändert. Die familiengeführte Unternehmensgruppe investierte 40 Mio. Euro, um ihre Kapazitäten zu erweitern und bestehende Anlagen durch hochmoderne zu ersetzen. Auf rund 25.000 Quadratmetern können im neuen Produktionswerk nun XXL-Teile gefertigt und vormontiert werden, die in Tittmoning allesamt auch vorbehandelt und beschichtet werden.
Die Hightec-Pulverbeschichtungsanlage
Den zunehmenden Ausmaßen der Bauteile trägt auch die neue Pulverbeschichtungsanlage Rechnung. Sie umfasst eine Pulverkabine mit 14 Automatikpistolen (7 pro Seite), weiteren zwei Pistolen unten sowie einer Handapplikation für Nachbeschichtungen. Außerdem ist eine Bypassstrecke für die Zweifachbeschichtung integriert.
„Die Anlage ist auf große Werkstücke bis sechs Metern Länge und mit einem Gewicht von bis zu 1.000 Kilogramm ausgelegt“, erläutert Benedikt Seidel, Lackiermeister und Hauptverantwortlicher für die Lackiertechnik bei Brückner in Tittmoning, „obwohl wir hier natürlich auch kleine, gerade einmal handgroße Teile beschichten.“
Herzstück der Brückner-Produktion sind die Spannrahmen
Auf die Frage, warum Brückner als Nasslackexperte in eine Pulverbeschichtung investiert hat, erklärt Seidel: „Die Bauteile bestehen aus verzinktem Stahl, feueraluminiertem Blech, Schwarzstahl, Stahlguss und Edelstahl.
Die fertigen Produkte sind bei unseren Kunden täglich einer sehr sauren und aggressiven Atmosphäre ausgesetzt – das sind harsche Bedingungen, die zu beschleunigter Rostbildung führen. Deshalb beschichten wir seit 2018 Maschinenbauteile mit Pulverlack, damit lassen sich die sehr hohen Anforderungen an eine Korrosions- und Chemikalienbeständigkeit erfüllen.“ Als weiteren Vorteil seien die Lösungsmittelfreiheit beim Pulverlackieren zu nennen, denn die vergleichbare Menge Nasslack würde rund fünf Tonnen Lösungsmittel (VOC) beinhalten.
Als Beispiel für eine Pulverapplikation nennt Seidel den Spannrahmen von Brückner, das „Herzstück“ in der Textilveredlung. Ein solcher Spannrahmen hat Arbeitsbreiten bis zu sieben Meter und ist 20 bis 30 Meter lang. „Er entwickelt sich zunehmend zur Multifunktionsanlage für die Herstellung technischer Textilien und sonstiger bahnförmiger Materialien. Täglich werden darauf in der ganzen Welt unzählige Meter verschiedenster Warenarten gespannt, getrocknet, thermofixiert, funktionalisiert und beschichtet“, weiß der Lackiermeister.
Die Spannrahmen müssen deshalb höchsten Qualitäts- und Leistungsanforderungen gerecht werden. Die einzelnen Bauteile für die Spannrahmen werden im eigenen Werk pulverbeschichtet. Dazu wurde in eine neue Pulverbeschichtungsanlage investiert: Die Wagner Pulveranlage mit ihren Automatikpistolen übernimmt gut 80 Prozent der Applikation, die restlichen 20 Prozent – die schwer zugänglichen Stellen – werden von einem der Nachbeschichter manuell aufbereitet.
Um eine Größenvorstellung von den zu beschichtenden Bauteildimensionen zu erhalten, fährt Seidel fort: „Für die riesigen Querrahmen benötigt man die gesamte Trägergröße der Beschichtungsanlage; bei Seitenrahmen passen zwei Bauteile auf einen Träger.“
Die Familie der PaintChecker mobile
Kompakter Controller und ultra-leichter Messkopf
Das komplette Messystem besteht aus zwei Einheiten: Dem Controller mit der Auswerte-Elektronik und dem leichten, kompakten Sensor als eigentlichem Messgerät. Die geringen Abmessungen des kleinsten Sensors von 130 × 25 mm bei gerade einmal 50 g Gewicht ermöglichen Messungen an Stellen, die bislang schwer zugänglich waren. Für jede Aufgabe der passende Sensor Die mobilen OptiSense Laser-Modelle werden vorwiegend für glatte Beschichtungen auf metallischem Untergrund eingesetzt. Die schlanken Laser-Sensoren eignen sich durch ihren winzigen Messfleck besonders für Schichtdickenprüfungen an filigranen Kleinteilen, Ecken und Kanten. Durch den größeren Messpunkt sind LED-Sensoren ideal für Freihandmessungen an rauen Oberflächen. Das Modell PaintChecker mobile Gun-R eignet sich dabei besonders für Bauteile aus Kunststoff oder Gummi.
Der PaintChecker mobile Gun-B ist für die berührungslose Prüfung von frisch aufgetragenen Pulverbeschichtungen vor dem Einbrennen optimiert. Er misst die noch weiche Pulverschicht farb- und sortenunabhängig auf Träger– materialien wie Metall, Glas oder Kunststoff. Dabei wird die Schrumpfung während des Aufschmelzens berücksichtigt.
Schichtdickenprüfung in der Automation
Die Schichtdicke der Spannrahmenanlagen soll zwischen 80 und 100 µm liegen. Für die Qualitätssicherung ist dabei der Nachbeschichter verantwortlich. „Er prüft die Rahmenbauteile auf die korrekte Schichtdicke und stellt unmittelbar fest, ob eine Düse verstopft ist oder die zu beschichtende Stelle von der Automatik nicht erreicht wurde“, so Seidel.
Die Bauteile der Brückner-Maschinen werden in den Standardfarben Lichtgrau und Signalgrau beschichtet. „Bei diesen automatisierten Pulverapplikationen läuft der Prozess rund. Die Schichtdicke ist gut eingepegelt“, stellt der Abteilungsleiter zufrieden fest, „lediglich bei Bauteilen mit vielen Unterschneidungen oder wenn die Bauteilgeometrie einen Faraday’schen Käfig bildet sind Stichprobenprüfungen wichtig. „Da kann es durchaus passieren, dass das Pulver nicht überall gleichmäßig verteilt wurde“, weiß Seidel. In solchen Fällen kommt auch an der automatisierten Pulveranlage regelmäßig der PaintChecker zum Einsatz.
Der Pulverer prüft, ob die Mindestschichtdicke von 80 µm erreicht wurde. Wenn nicht, wird manuell nachgepulvert. „Die Atline-Prüfung ist deutlich kostengünstiger und auch deutlich weniger zeitintensiv. Wenn bei einem Bauteil erst nach dem Trockenofen eine fehlerhafte Schichtdicke festgestellt wird, muss dieses Teil eine komplette Ehrenrunde in der Anlage drehen“, bringt Seidel die kostenintensive Nachbeschichtung ohne Paint-Checker „Frühwarnsystem“ auf den Punkt und erinnert sich an einen Lohnbeschichtungsauftrag, welcher der Auslöser für die neue Qualitätskontrolle von OptiSense im Hause Brückner war.
Auf die richtige Pulvermenge kommt es an
2020 erhielt die Brückner Gruppe einen großvolumigen Lohnbeschichtungsauftrag über Isolierplatten mit einem ableitfähigen Lack. Die isolierten 60×60 cm Platten kommen im Messebau und in Reinräumen von Krankenhäusern und Laboren zum Einsatz. Diese quadratischen Isolierplatten sollten in den Weißtönen Ral 9010 und 9016 beschichtet werden, die Toleranzgrenzen der Schichtdicke hatte der Kunde vorab mit 80 und 100 µm definiert. Der vorgegebene Pulverlack war neu auf dem Markt.
„Jedes Pulver lässt sich anders verarbeiten. Sogar identische Farbtöne bedingen je nach Hersteller verschiedenen Mengen an Pulverausstoß. Es ist ein steter Lernprozess, wie viel Pulver ausgestoßen werden muss, um die 80 µm Schichtdicke zu erhalten“, beschreibt der Abteilungsleiter die Hintergründe. „Damals konnten wir die Bauteile erst nach dem Einbrennen messen. Da kann dann nicht mehr manuell nachbeschichtet werden. Die Teile, die unter- oder überbeschichtet waren, mussten entsorgt werden“, blickt Seidel zurück: „Und durch den mannigfaltigen Ausschuss hat sich der Auftrag natürlich überhaupt nicht gerechnet. Wir haben nach diesen Erfahrungen unmittelbar recherchiert, ob es ein Messgerät gibt, mit dem wir die Schichtdicke früher, also vor dem Einbrennen, messen können.“
Schnell wurde der Abteilungsleiter fündig: Der PaintChecker mobile von OptiSense schien ein aussichtsreicher Kandidat zu sein. Sales Manager Sascha Schmidt präsentierte schon bald das Gerät im neuen Oberflächenbeschichtungszentrum von Brückner Textile Technologies. Zudem konnten das 16-köpfige Lackierteam um Benedikt Seidel das Prüfgerät in der eigenen Produktion zwei Wochen auf Herz und Nieren prüfen. „Ja, es gab einen Mitbewerber. Aber dessen Gerät blitzte bei jeder Messung. Und wenn ein Mitarbeiter 200 Messungen macht, hat er am Ende des Tages Sternchen vor Augen. Zudem konnten wir mit dem Gerät gar nicht unmittelbar nach der Kabine messen, weil der Blitz sofort unsere Löschanlage auslöste.“ Die Entscheidung pro OptiSense war daher schnell gefallen.
Der PaintChecker als virtueller Lehrmeister
Während im automatisierten Prozess lediglich Stichproben von „kniffligen“ Teilen mit dem PaintChecker mobile überprüft werden, ist die Qualitätskontrolle in der Handbeschichtung deutlich intensiver. „Das liegt in der Natur der Sache, denn hier werden Sonderbauteile mit verschiedensten, teilweise auch ganz neuen Pulvern beschichtet. Bei den Sondermaschinen und Sonderfarben liegen die Idealwerte der Schichtdicke bei 60 µm für die Grundierung und bei 80 µm für den Decklack. Es gibt also keine standardisierten Prozessabläufe“, erklärt Seidel die Unterschiede.
Zudem hat das Schichtdickenmessgerät in der manuellen Applikation noch eine weitere Funktion: der PaintChecker ist quasi ein virtueller Lehrmeister. Neue, teilweise noch wenig erfahrenen Mitarbeiter können so selbst die Qualität ihres Pulverauftrags prüfen. Unmittelbar nach der manuellen Applikation – in noch weichem Pulverzustand – misst der Mitarbeiter seinen Beschichtungsauftrag nach und kann diesen schnell und einfach korrigieren. Und auch die alten Lackhasen in Seidels Team bauen auf den PaintChecker. Sie prüfen ebenfalls Atline und wissen, wenn die Schichtdicke beim weich gemessenen Pulver in Ordnung ist, brauchen sie keinen Gedanken mehr daran zu verschwenden, ob die Beschichtung auch nach dem Einbrennen noch passt. „Warum? Wir haben Kontrollmessungen mit einem berührungsbehafteten Messgerät durchgeführt – die Messwerte vom PaintChecker mobile und der kontakt behafteten Referenzmessung stimmten zu 100 Prozent überein“, belegt Seidel.
Der PaintChecker als Lieblingsgerät der Mitarbeiter
Die Messreihen vom mobilen Handgerät werden auf dem PC abgelegt. Diese Dokumentation dient Brückner bei möglichen Reklamationen als Nachweis und auch dem Kunden für seine Archivierung. Zudem werden die Daten hinsichtlich des jeweiligen Pulververbrauchs ausgewertet. Seidel: „Jährlich verbrauchen wir rund 35 Tonnen Pulver. Wir haben den Pulververbrauch dank der frühzeitigen Messungen mit dem PaintChecker deutlich reduzieren können. Weniger Ausschuss bedeutet weniger Pulver und damit minimierte Kosten.“ Nach seinem Fazit gefragt, schmunzelt Benedikt Seidel wissend: „Der PaintChecker mobile erleichert die Arbeit enorm – es ist das Lieblingsgerät meiner Mitarbeiter.“
Die Brückner Gruppe
Das weltweit agierende Maschinenbauunternehmen entwickelt, produziert und vertreibt seit 1949 Maschinen und komplette Anlagen für die Veredlung von technischen Textilien sowie Bekleidungstextilien, Glasfasergewebe, Vliesstoffe und Bodenbelägen. Zudem konstruiert der Markt- und Technologieführer Sondermaschinen und Anlagen zur Wärmerückgewinnung bzw. Abluftreinigung. Die Brückner Gruppe eröffnete 2013 ihr Technologiezentrum in Leonberg, 2018 wurde das Produktionswerk in Tittmoning eingeweiht. An den beiden deutschen Standorten erwirtschaften rund 420 Mitarbeiter einen Jahresumsatz von über 100 Mio. Euro. Seit 2020 gibt es zudem ein Büro in Shanghai.
OptiSense GmbH & Co. KG
Annabergstraße 120
45721 Haltern am See
Telefon: +49 (5254) 933343
http://www.optisense.com
Telefon: +49 (163) 3933343
E-Mail: hostmann@optisense.com