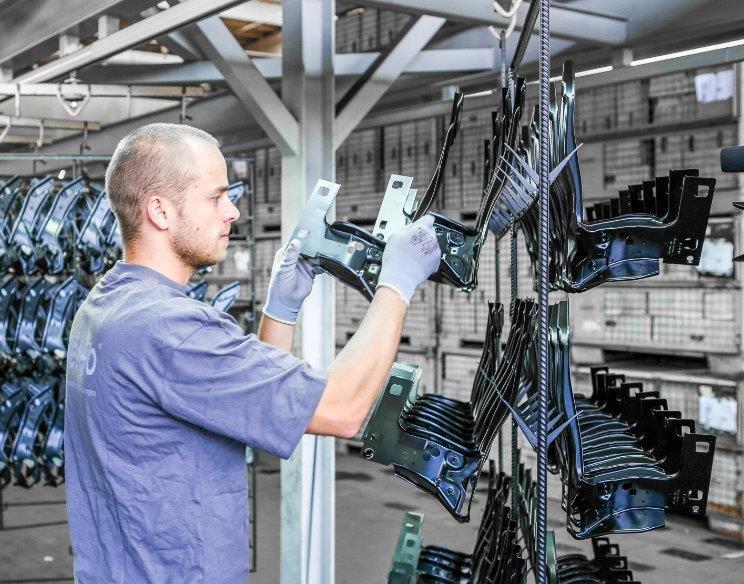
Die Redaktion besuchte die Metob Unternehmensgruppe und sprach mit dem geschäftsführenden Gesellschafter Marco Jobst und dem Qualitätsleiter Martin Kolenda über die Herausforderungen der anspruchsvollen Beschichtung aus der Automotive-Industrie.
Mitarbeiter als Erfolgsfaktor
Auf die Frage, was die Metob Unternehmensgruppe auszeichnetet, antwortet Marco Jobst sofort „unsere Mitarbeiter“. Die Verfahrensmechniker für Beschichtungstechnik seien wirkliche Fachkräfte und viele von ihnen hätten hier bereits ihre Ausbildung absolviert, so der geschäftsführende Gesellschafter weiter.
Dass bei Metob heute zahlreiche Stellen im Qualitätsmanagement und in der Fertigung durch ehemalige, eigene Auszubildende besetzt sind, ist ein Verdienst des langjährigen Qualitäts- und Ausbildungsleiters Martin Kolenda, der als Kfz-Meister und Umwelttechniker Verfahrenstechnik viel Knowhow an die Azubis weitergeben kann. Mit großem Praxisbezug lernen die Auszubildenden, wie man die Anlagenparameter für eine perfekte Oberfläche steuert.
Dieses Wissen gepaart mit der langjährigen Erfahrung des Teams ist bei den insgesamt acht Linien – vier Pulver- und drei KTL-Beschichtungsanlagen sowie eine Anlage zum Waschen, Beizen und Konservieren – ein nicht zu unterschätzender Wettbewerbsfaktor.
Acht Anlagen für unterschiedlichste Beschichtungsaufgaben
Allein in der Pulverbeschichtungstechnik reicht das Spektrum der Metob-Anlagen von einer kleinen Handbeschichtung über die Automatikkabinen für Serienteile bis hin zur vollautomatischen, komplexen Beschichtungsanlage; letztere mit einer großen Vorbehandlungsstrecke. So kann jeder einzelne Kundenauftrag hochwirtschaftlich und nachhaltig produziert werden.
Die Kunden stammen vor allem aus dem Automotive-Umfeld sowie aus der Möbel- und Kinderwagenindustrie. Für die Automobil-Klientel werden auf der vollautomatisierten Pulveranlage „Nummer 4“ täglich Führungsschienen für PKW-Fensterheber beidseitig beschichtet.
Die effiziente Reise der Bauteile durch die Beschichtungsanlage
Nachdem die Führungsschienen angeliefert und vereinnahmt worden sind, begeben sich die Substrate auf eine gut 200 Meter lange Reise durch die Kreislaufförderanlage. Dazu hängen Mitarbeiter der Fertigung die Teile auf eigens dafür entwickelte Beschichtungsvorrichtungen auf.
Nun fahren die Teile nach oben. Dort werden sie von Fett sowie Schmutz befreit und mit einer Konversionsschicht überzogen, die als Korrosionsschutz bzw. Haftvermittler dient. Nach der Vorbehandlung werden die Führungsschienen gespült und getrocknet, um eine optimale Oberflächenreinheit zu garantieren. Jetzt transportiert das Förderband die Substrate zum Herzstück der Pulverapplikationsanlage, der Beschichtung. Hier erfolgt die vollautomatisierte Applikation des Pulverlacks. Pistolen beschichten beide Seiten des Bauteils; die A-Seite der Führungsschiene wird separat zur B-Seite mit dem Pulverlack versehen.
Die intelligente Lückensteuerung erkennt Anfang und Ende der Gehänge. Auf diesen bauteilfreien Zwischenräumen schalten sich die Pistolen automatisch aus. Damit wird Pulver gespart. Überschüssiges Pulver wird dem Kreislauf wieder zugeführt.
Hohe Herausforderung im Beschichtungsprozess
Die Anforderung in diesem automatisierten Beschichtungsprozess liegt im rückwärtigen, abgewandten Bereich der Führungsschiene. Hier gilt es, möglichst die gleiche Schichtdicke zu erzielen wie auf der Vorderseite des Bauteils.
„Die Führungsschienen sind sehr kleine, komplexe Teile mit unterschiedlichsten Geometrien. Zudem sind wir nach oben und unten in der Schichtdicke begrenzt“, beschreibt Martin Kolenda die Herausforderungen des Lohnauftrags. „Das Toleranzband von 40 bis 120 μm sieht auf den ersten Blick zwar recht komfortabel aus, die Tücke liegt aber im Detail: Denn Vorder- und Rückseite der Füh-rungsschienen müssen eine annähernd gleiche Schichtdicke aufweisen.“
Wenn zu viel Pulver bei den Führungsschienen aufgetragen wird und die Schichtdicke damit außerhalb des Toleranzbandes liegt, klemmen die PKWFenster später beim Öffnen. „Denn der Mechanismus kann die Fensterscheibe nicht mehr nach oben befördern. Und im schlimmsten Fall macht der elektrische Motor des Fensterhebers schlapp, weil er einfach zu viel Kraft benötigen würde, um die verklemmte Scheibe zu bewegen“, weiß der Qualitätsleiter.
Doch damit nicht genug der Herausforderungen: Metob verarbeitet zahlreiche verschiedene Schienenpaare, die auch noch völlig unterschiedliche Geometrien aufweisen. Hinzu kommen variable, externe Einflüsse wie Luftfeuchtigkeit oder Temperatur, die sich ebenfalls auf die Beschichtung auswirken.
Um die störenden Außeneinflüsse auszugleichen, können die Parameter der Beschichtungsanlage zwar angepasst werden, dennoch bleibt die Beschichtung der Führungsschienen ein äußerst fragiler Prozess.
Pro Tag beschichtet die Anlage eine hohe Anzahl solcher Führungsschienen. Mit den bisherigen Prüfgeräten wurde die Schichtdicke nach dem Einbrennen, also sehr spät im Prozess, gemessen.
Die Familie der PaintChecker mobile
Kompakter Controller und ultra-leichter Messkopf
Das komplette Messystem besteht aus zwei Einheiten: Dem Controller mit der Auswerte-Elektronik und dem leichten, kompakten Sensor als eigentlichem Messgerät. Die geringen Abmessungen des kleinsten Sensors von 130 × 25 mm bei gerade einmal 50 g Gewicht ermöglichen Messungen an Stellen, die bislang schwer zugänglich waren.
Für jede Aufgabe der passende Sensor
Die mobilen OptiSense Laser-Modelle werden vorwiegend für glatte Beschichtungen auf metallischem Untergrund eingesetzt. Die schlanken Laser-Sensoren eignen sich durch ihren winzigen Messfleck besonders für Schichtdickenprüfungen an filigranen Kleinteilen, Ecken und Kanten.
Durch den größeren Messpunkt sind LED-Sensoren ideal für Freihandmessungen an rauen Oberflächen. Das Modell PaintChecker mobile Gun-R eignet sich dabei besonders für Bauteile aus Kunststoff oder Gummi.
Der PaintChecker mobile Gun-B ist für die berührungslose Prüfung von frisch aufgetragenen Pulverbeschichtungen vor dem Einbrennen optimiert. Er misst die noch weiche Pulverschicht farb- und sortenunabhängig auf Trägermaterialien wie Metall, Glas oder Kunststoff. Dabei wird die Schrumpfung während des Aufschmelzens berücksichtigt.
„Wenn sich dann erst herausgestellt hat, dass die Schichtstärke nicht stimmt, war die gesamte Strecke nach der Applikation Verlust. Denn die Parameter, die in der Anlage eingestellt sind, gelten für die gesamte Charge. Eine große Menge wäre fehlbeschichtet und müsste kostenintensiv entsorgt werden“, rechnet Jobst vor.
Um die Prozesseinstellungen und die Prozesssteuerung zu optimieren, setzt die Unternehmensgruppe jetzt auf eine Schichtdickenmessung schon vor dem Einbrennen des Pulverlacks.
Durch den OptiSense-Anwenderbericht in einer Fachzeitschrift war der Metob- Geschäftsführer auf die prozessbegleitende Schichtdickenprüfung aufmerksam geworden. „Berührungslos vor dem Einbrennen klang sehr spannend“, erinnert sich Marco Jobst, „ich habe dann einfach bei OptiSense angerufen“.
PaintChecker besteht Probezeit
OptiSense-Mitarbeiter Sascha Schmidt führte das Schichtdickenprüfsystem PaintChecker Mobile fluchs vor. Anschließend wurde das Handmessgerät von Metob-Mitarbeitern im laufenden Betrieb ein Vierteljahr auf Herz und Nieren geprüft und mit den Messwerten der berührungsbehafteten Geräte nach dem Aushärten verglichen. „Letztlich wollten wir ja wissen: Ist die Anlage wirtschaftlich eingestellt? Denn nur so können wir Reklamationen und Fehlbeschichtungen vermeiden“, bringt es Qualitätsleiter Kolenda auf den Punkt.
Natürlich schaute sich Metob auch bei Mitbewerbern in Sachen Messtechnik um. „Die Geräte haben bestimmt auch ihre Berechtigung – für uns waren sie aber wenig geeignet. Der Messfleck der Geräte war zu groß und damit die Messwerte nicht so genau wie wir es uns gewünscht hätten. Deshalb hat OptiSense das Rennen gemacht“, resümiert Kolenda die Entscheidung pro PaintChecker Mobile. Das Unternehmen orderte zunächst zwei der mobilen Messgeräte.
“„Ich kann mit dem Paint Checker wirklich Schichtdicken ganz einfach und sofort messen – ohne komplexe Einarbeitung.“
Marco Jobst, Geschäftsführender Gesellschafter, Metob Unternehmensgruppe
Die frühe Messung erspart Fehlbeschichtungen
Jetzt prüft ein Beschichter aus dem Fertigungsteam jeweils direkt hinter der Beschichtungskabine die Schichtstärke, wenn der Pulverlack noch nicht eingebrannt ist. Bei einer Beschichtung außerhalb der Toleranz kann nun viel schneller reagiert und die Anlageneinstellung korrigiert werden.
Geprüft wird pro Führungsschiene an sechs „neuralgischen“ Punkten, die entsprechend gekennzeichnet sind. Dazu entnimmt ein Mitarbeiter die Schiene aus dem Produktionsprozess. Er misst die Schichtdicke und dokumentiert diese, um abschließend Soll- und Ist-Werte zu vergleichen. Die Endergebnisse werden dokumentiert und archiviert.
Alle 15 Minuten werden Kontrollmessungen der Schichtdicke durchgeführt. Metob setzt auf eine äußerst intensive serienbegleitende Prüfung, bei der in eng getakteten Zeiträumen Schichtdicke und Glanzgrad gemessen sowie Haftungsprüfungen (Gitterschnitt) durchgeführt werden.
„Wir werden heutzutage in Sachen Nachweispflicht stark gefordert. Das ist den speziellen Anforderungen der unterschiedlichen Aufträge geschuldet. Je nach Kunde gibt es zudem noch weitere Auflagen wie Zugscherprüfung, Lichtbogen-, sowie Peel-Test und Korrosionsprüfungen. Wir führen all diese Tests Inhouse durch und archivieren abschließend die Prüfberichte. Zudem lagern wir noch Rückstellmuster zum eventuellen späteren Abgleich ein“, erklärt Jobst die Notwendigkeit einer lückenlosen Dokumentation.
Stabile Prozesse durch intensive, serienbegleitende Prüfung
„Seitdem wir den PaintChecker Mobile nutzen, sind unsere Prozesse deutlich stabiler geworden“, bestätigt Martin Kolenda, „früher konnten wir die Schichtdicke erst nach dem Einbrennen messen; mit der berührungslosen Prüfung vor dem Einbrennen sind die Schwankungsamplituden deutlich geringer.“
Inzwischen konnte das Toleranzband der Schichtdicke harmonisiert werden. Und auch die Egalisierung der Schichtdickenwerte von Vorder- und Rückseite ist gelungen. Die Werte unterscheiden sich nur noch um wenige μm und es gibt kaum mehr Ausreißer. Der Prozess läuft gleichmäßiger und besser.“
Das neue Prüfverfahren rechnet sich
Eine nachhaltige Produktion schreibt Metob in großen, grünen Lettern – nicht nur, wenn es um lösungsmittelfreie Lacke geht. Schließlich ist es ein energieintensives Unternehmen mit einem Stromverbrauch von rund 4 Mio. kWh und einem Gaskonsum von zirka 14 Mio. kWh pro Jahr.
Die Energiewende hat Metob längst geschafft: 2016 wurde ein Blockheiz-kraftwerk in Betrieb genommen. 2020 ging die Photovoltaikanlage an den Start, die gerade erweitert wird und schon jetzt einen wesentlichen Beitrag zur Reduzierung der CO₂-Emission leistet. Seit 2020 speist das Unternehmen seinen Stromverbrauch komplett aus erneuerbaren Energien. 2021 wurde ein Kompensationsprojekt für Erdgas initiiert.
„Der PaintChecker garantiert stabilere Prozesse, weniger Ausschuss und wir sparen damit eine Menge Ressourcen ein.“
Martin Kolenda, Umwelttechniker Verfahrenstechnik, Ausbildungs- und Qualitätsleiter, Metob Unternehmensgruppe
„Durch den Einsatz der Grünstromprodukte sind wir im Scope 2 – das sind Emissionen aus der Nutzung von Energie, die wir einkaufen – jetzt schon klimaneutral“, freut sich Marco Jobst. Inzwischen hat die Unternehmensgruppe zudem einen Energieberater beauftragt, der in einem Audit weitere Einsparpotenziale aufzeigen soll.
„Durch das neue Schichtdickenmessgerät wissen wir viel schneller, ob unsere Beschichtung in Ordnung ist oder nicht. Und jedes Teil, das wir heute nicht mehr entsorgen müssen, bedeutet weniger Anlagenbelastung, Energieverbrauch, Ressourceneinsatz und Materialverlust. Wir sparen mit dem PaintChecker Mobile also gleichzeitig Rohstoffe und Energie ein.“
Mittlerweile hat Metob übrigens zwei weitere PaintChecker Mobile für das Werk in Hildburghausen (Thüringen) angeschafft. Unter dem Strich steht jetzt dank OptiSense die vierfache Optimierung in Sachen Resourceneffizienz.
Die Metob Gruppe
Die Metob Unternehmensgruppe gehört mit ihren KTL- und Pulverbeschichtungen sowie der Beizpassivierung zu den leistungsfähigsten und vielseitigsten Oberflächenveredlern in Deutschland. An den Standorten Michelau (Oberfranken) und Hildburghausen (Thüringen) sind auf rund 20.000 m² Produktionsfläche mehr als 250 Mitarbeiter verantwortlich für die Qualität von Oberflächen.
Eigene Entwicklungen, modernste Anlagentechnik und eine leistungsfähige Logistik orientieren sich bei Metob stets an Nachhaltigkeit und Ressourceneffizienz, denn umweltgerechtes Handeln hat einen wichtigen Platz in der gelebten Unternehmenspolitik.
OptiSense GmbH & Co. KG
Annabergstraße 120
45721 Haltern am See
Telefon: +49 (5254) 933343
http://www.optisense.com
Telefon: +49 (163) 3933343
E-Mail: hostmann@optisense.com